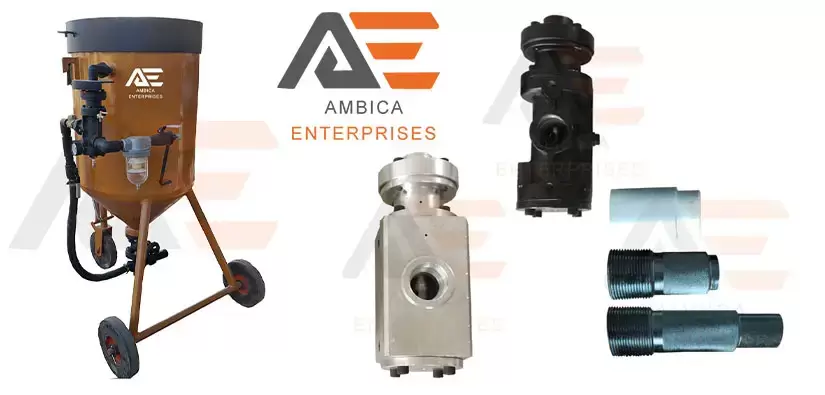
For effective functionality sand blasting, it has become compulsory to know about the sand blasting machine’s equipment and its operation processes. Sand blasting machine is also called abrasive blasting Machine. Sand blasting process is the procedure of forcibly launching a stream of abrasive material such as sand, grit, shot, etc against a surface under high pressure to smooth a rough surface, roughen a smooth surface and shape a surface, or eliminate the surface contaminants. There are different variants of its process, such as sand blasting, portable shot blasting and grit blasting, abrasive blasting, etc.
Sand blasting method or how it works?
The abrasive is collected in the pressure pot then sealed. It is metered into the blast hose and conveyed by the compressed air through the blast nozzle. Sand blasting is typically utilized to generate a surface profile when the frictional heat of dry blasting would damage the element.
Wheel blasting:
Wheel blasting machines are a high-power, high-efficiency blasting performance with recyclable abrasive material. Functional wheel blast machines propel plastic media abrasive in a cryogenic pot; this type of wheel blasting is normally utilized for deflating plastic and rubber components. The size of the wheel blast machine and the number and power of the wheels depending on the elements to be blasted and on the required result and efficiency.
Hydro-blasting:
It is generally seen as water blasting, is a common abrasive blasting operation because it is very effective and, in most cases, will only need one operator. In this process, water is utilized to remove chemicals, old paint, or buildup without damaging the previous surface. The hydro-blasting method is ideal for cleaning internal and external surfaces because the operator is commonly able to send the stream of water in places that previously were believed unreachable.
Blast room:
The blast room has three of the four components of a blast cabinet. maximum blast room have recycling systems ranging from standard recycling to full reclaim floors that carry the abrasive pneumatically or mechanically to a device that cleans the abrasive prior to recycling.
Micro-abrasive blasting:
Micro-abrasive blasting uses smaller nozzles to give a fine stream of abrasive perfectly to either a small part of a small area on a larger part. Usually, the area to be blasted is from about 1 mm to only a few cms at most as abrasive (sand) blasters with bigger nozzles are faster for larger areas.
However, the equipment for sand blasting usually consists of but is not bounded to a hand-held nozzle that directs a stream of abrasive media. Therefore abrasive is mixed with air in a mixing chamber in order to transport it to the nozzle where it is subject to a high-velocity air
Sand blasting Machine’s Operation:
Sand blasting is a method of impelling abrasion using compressed gas or pressurized liquid as the propellant. There are various generic terms for this application normally related to the abrasive media used. General terms include sand blasting, shot blasting, Abrasive blasting, and grit blasting.
The Sand blasting Operation Require a variety of Equipment:
Sand blasting Machine’s Equipment and How does it work are the following :
Portable blast equipment: Dry abrasive blasting purposes are powered by an air compressor. Most applications include a pressurized pot that contains the abrasive and meters it into the compressed air stream. Wet blasting is achieved by injecting the abrasive into a pressurized water stream or creating a slurry of abrasive and water that is pressurized or introduced into a compressed air stream.
Automated Blasting: Automated Blasting is an automated blasting that gives surface preparation and coating applications under cover to minimize the effects nature can have on prepared steel, with minimum or no impact on the environment.
Blast cabinet: A typical blasting cabinet consists of four Equipment; the containment, the sand blasting system, the sand recycling system, and the dust collection. Basically, sand blasting cabinet is a closed-loop system in that an operator can blast the part and also recycle the abrasive media (sand). The operative blasts the components from the outside of the cabinet by placing his arms in gloves joined to glove holes on the cabinet, seeing the blasting component through the window, and typically, turning the blast on and off utilizing a foot pedal.
Types of blast systems used in a blasting cabinet:
Two systems that are utilized in the abrasive blasting cabinet are dry and one is a wet blast system that uses compressed air to create a vacuum in the blast gun. The negative pressure pulls abrasive into the blast gun where the compressed air directs the abrasive through the shot / sand blasting nozzle.
Typically these sand blasting machine consists of a mixer chamber in which sand and air both get mixed. Nozzles arrive in a variety of shapes, sizes, and substances (materials). Silicon carbide and boron carbide are more wear-resistant and are for use with more difficult abrasives such as aluminum oxide.